Flexible PCB(FPC): The new trend in electronic design
This article introduces the advantages, classification, and production process of flexible PCBs, compares the differences between flexible PCBs and traditional PCBs, and describes the applications of flexible PCBs.
Flexible PCB(FPC): The new trend in electronic design
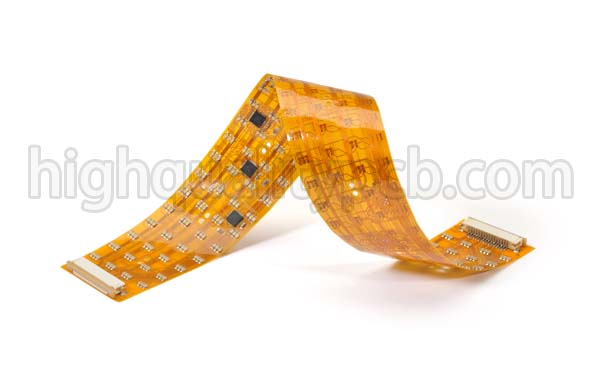
Abstract: With the continuous upgrading of products, traditional printed circuit boards can no longer
meet the needs of the PCB market, so flexible PCBs have been
introduced, and their market demand is growing. Medical, aerospace and consumer electronics use
FPCs.Flexible PCBs are magical circuit boards that can bend, wrap, and fold flexibly and move in a
narrow space like a snake. How does it do this? This article will reveal the answer to your question.
What is FPC?
Flexible circuit boards, also called soft boards. There are many insulating substrates for flexible
assembly, such as polyimide (PI), polyester film (PET), aramid fiber paper (Nomex), and polyvinyl
chloride (PVC).
By embedding circuit design on plastic sheets, more electronic
components can be arranged in order on the circuit board, thus realizing a flexible circuit
board. The birth of flex-PCB breaks through the traditional interconnection technology. It is popular
because of its lightweight, high flexibility, thin thickness, bendability, and foldability. It is easy
to install.
flexible printed circuit appeared in the United States in the 1970s to develop space rocket technology.
It is used in many fields due to its excellent properties.
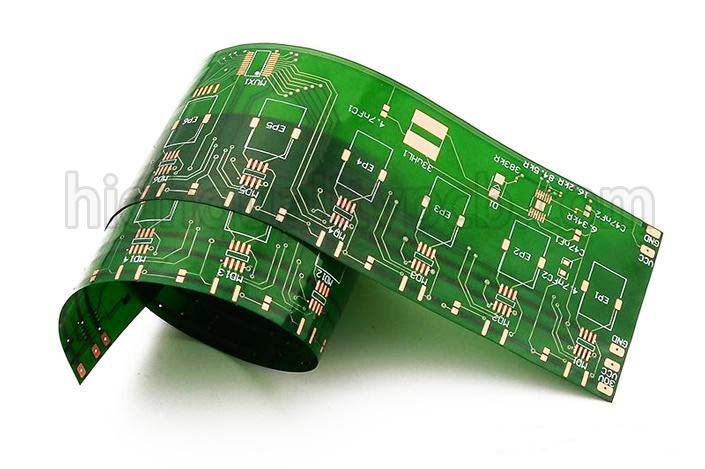
Advantages of FPC
1) High flexibility
This feature allows the circuit board to be bent and folded freely without damage. It can be arranged in
any spatial layout, moved, and stretched in a small space. It is conducive to SMT assembly.
2) Lightweight and thin
It makes the circuit board layout more compact, thus reducing the product size, reducing the product
weight, and making it easier to carry. It also promotes the development of high-density,
high-reliability, and miniaturization of electronic products.
If the product needs to consider the space question, then flexible circuit boards are the best choice.
3) Improve design flexibility
Due to its lightweight, thin thickness, and flexibility, there are multiple circuit board design plans
during circuit design. It increases the PCB's manufacturability, reliability, and performance.
In addition, flex pcb also has the advantages of good heat dissipation and solderability,
easy installation, and low overall cost.
Flexible circuit board classification
1) Single-sided flexible board
Use single-sided PI flexible copper-clad board material. After completing the circuit, cover it with a
protective film to form a single conductor circuit board. It has the lowest cost. When the electrical
performance requirements are not high or adopting single-sided wiring, single-sided flexible boards
should be selected—for example, printer inkjet cartridges and computer memory.
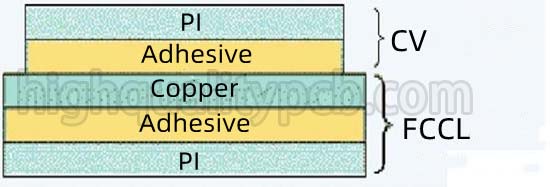
2) Double-sided flexible board
Use double-sided PI flexible copper-clad laminate material. After completing the circuit, a layer of
protective film is covered on both sides to form a dual-conductor circuit board.
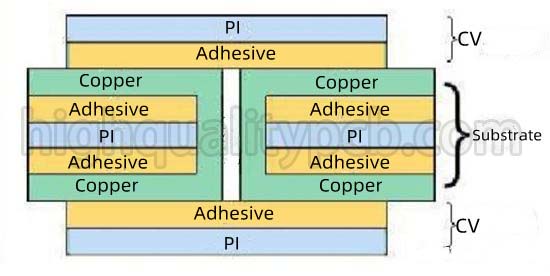
3) Multilayer flexible board
Multilayer flexible boards stack up three or more layers of circuit boards together, forming metalized
holes through drilling and electroplating to form conductive paths between layers. Although the number
of PCB layers is unlimited, we should consider component assembly and PCB manufacturability during PCB
layout design.
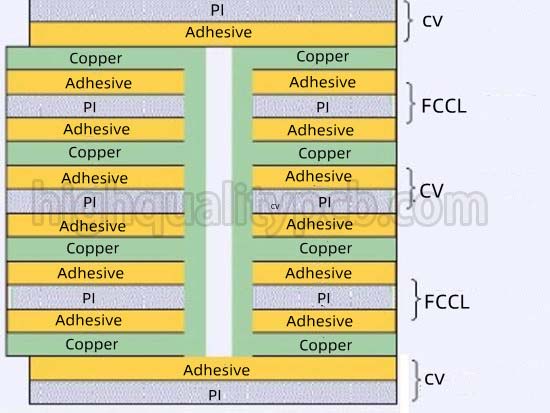
4) Rigid-Flex PCB
Rigid-flex PCB is a combination of rigid PCB and flex-PCB selectively stacked together. It has the
advantages of both rigid and flexible circuit board (bendability and sturdy rigidity). However, the
price is higher, so when manufacturing this PCB, you should consider reducing the number of layers.
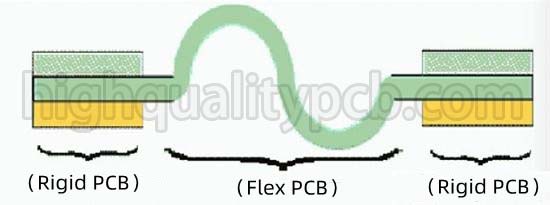
Flexible PCB Production Process
The production process here is for double-layer boards. The difference between the single-layer board
and the double-layer board process is that single-layer boards do not require drilling and metallization
holes.
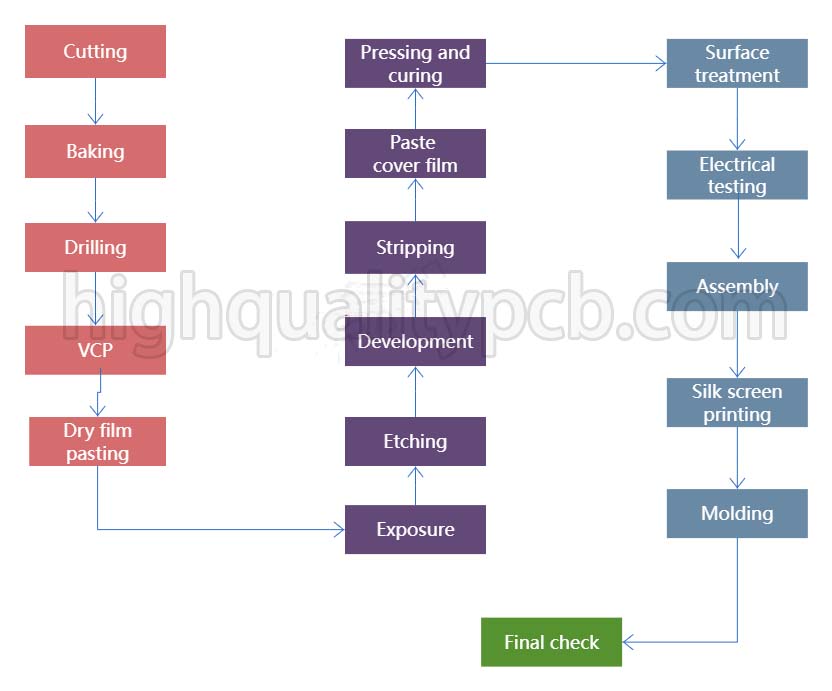
Cutting: Cut the material into the required size according to the work order size requirements. The
primary equipment is an automatic cutting machine and a manual cutting machine.
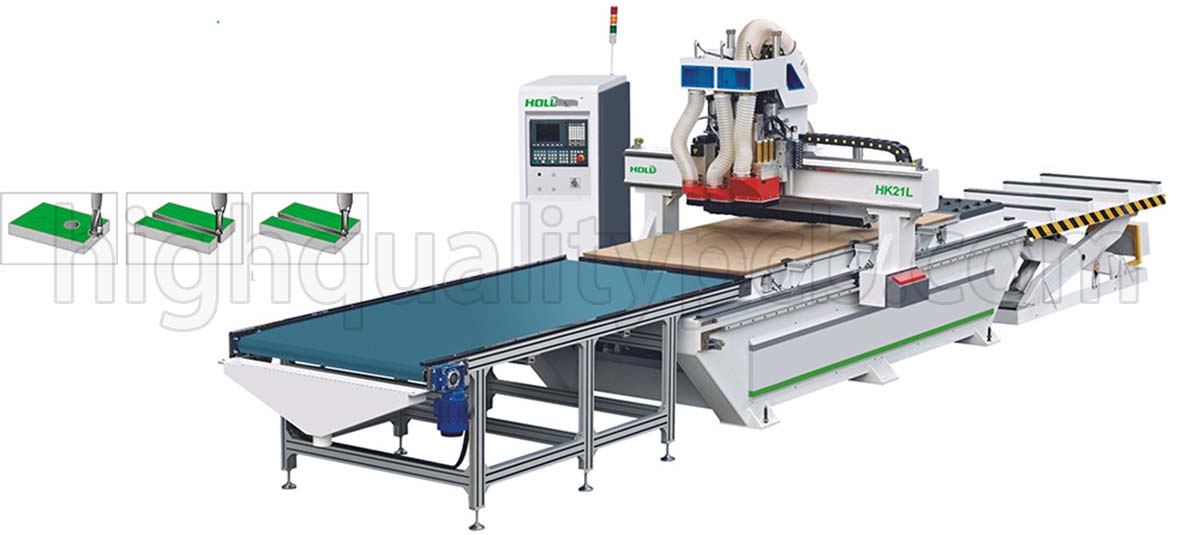
Baking: Dry the moisture in the substrate to avoid shrinkage, stratification, and other effects on
subsequent production. The equipment is an oven, and the working parameters are 120°C for 2 hours.
Drilling: It refers to drilling holes and vias on the substrate. It prepares for subsequent processes or
hole metallization. The primary device is a CNC drilling machine.
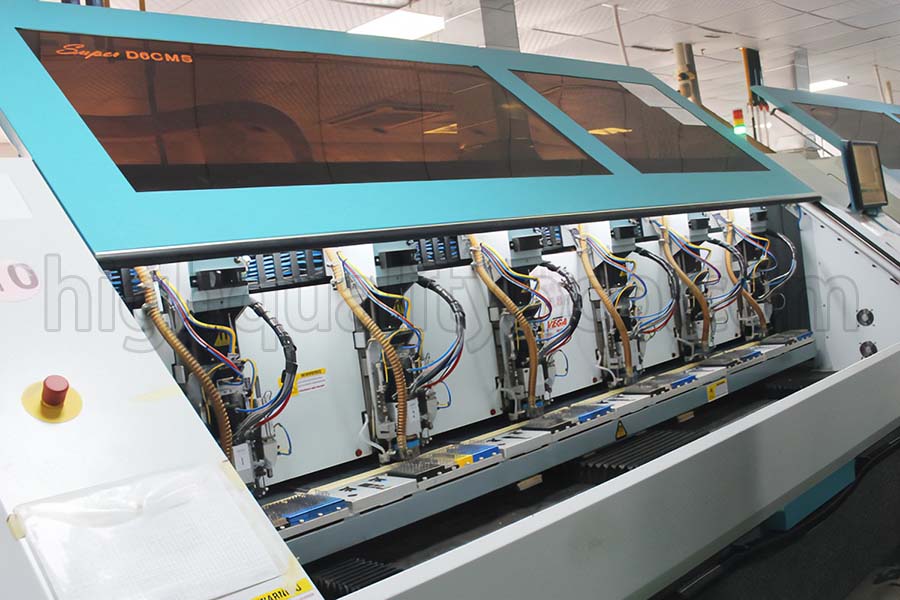
Black hole: Through the black hole in this step, a layer of conductive carbon powder is directly
deposited on the hole wall PI, replacing the traditional copper deposition. It prepares for copper
plating. The equipment is the black hole line.
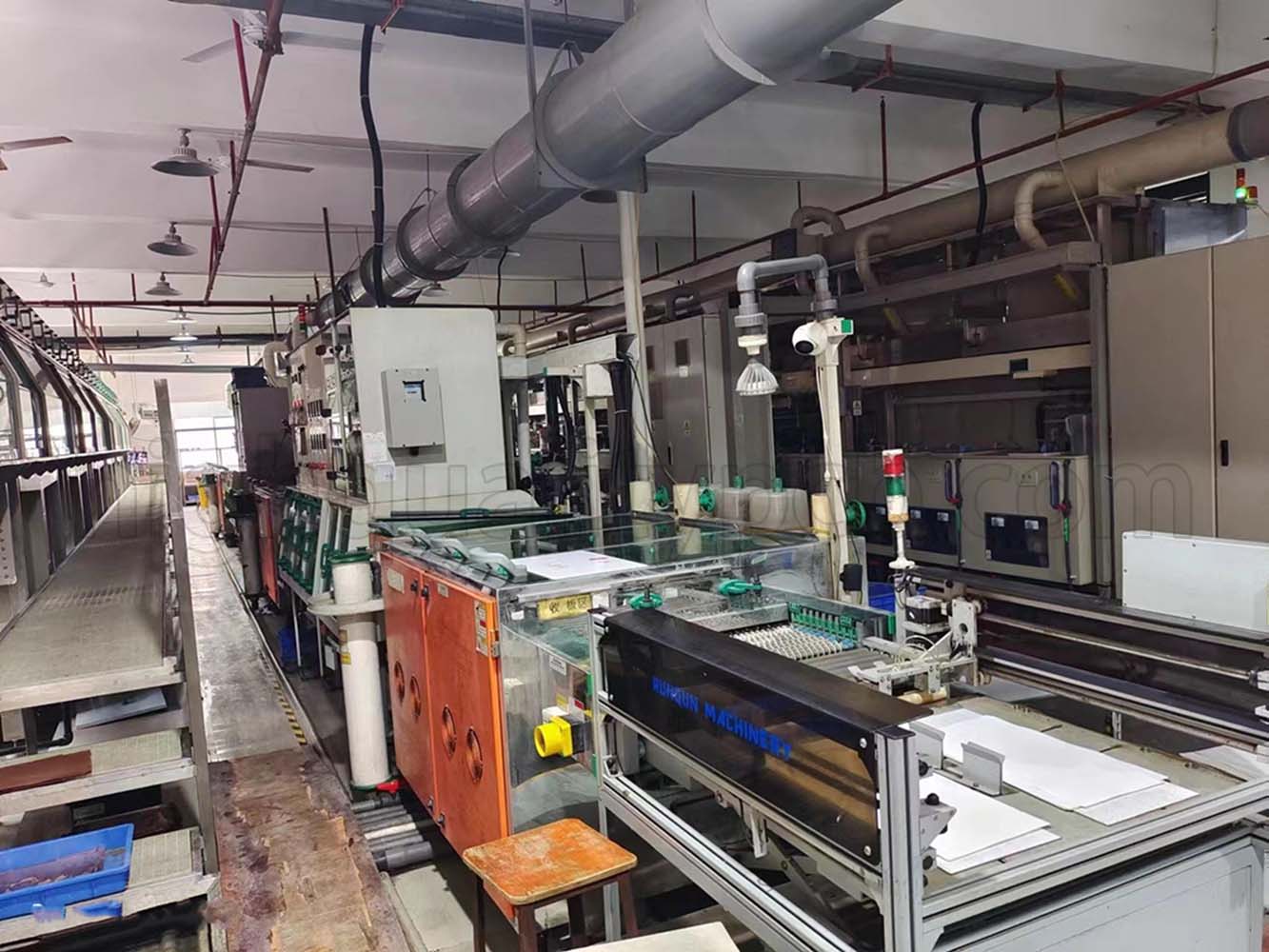
VCP: It's vertical conveyor plating, which uses copper electroplating to thicken the hole wall and
surface copper according to the customer's request.
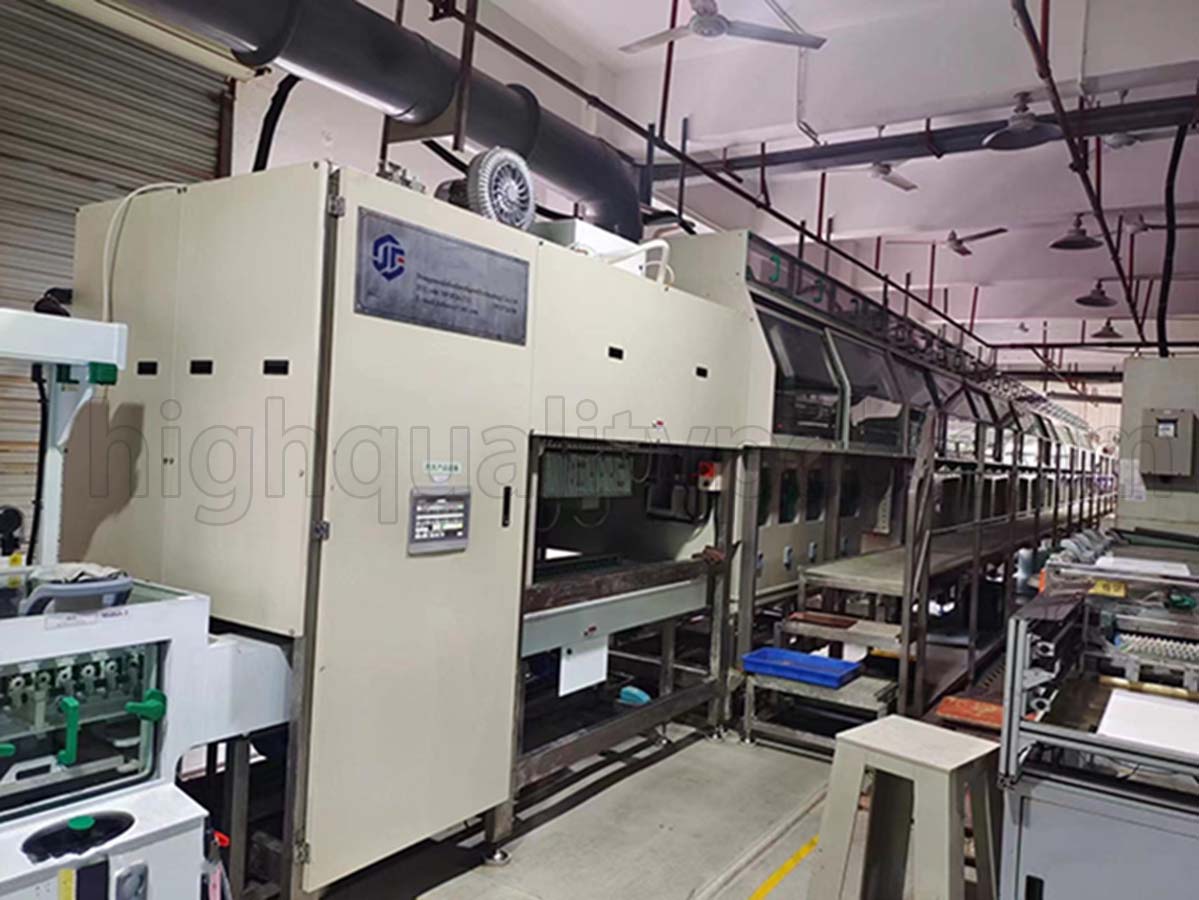
Dry film pre-treatment: Clean the board surface using chemical cleaning to remove oxidation and surface
roughening.
Dry film pasting: A layer of photosensitive dry film is pasted on the surface of the copper foil. They
are completing this step in a dust-free workshop, and the equipment is an automatic film-pasting
machine.
Exposure: According to the film exposure corresponding to the work order, the image of the circuit
pattern film is transferred to the dry film. The device is the automatic exposure machine.
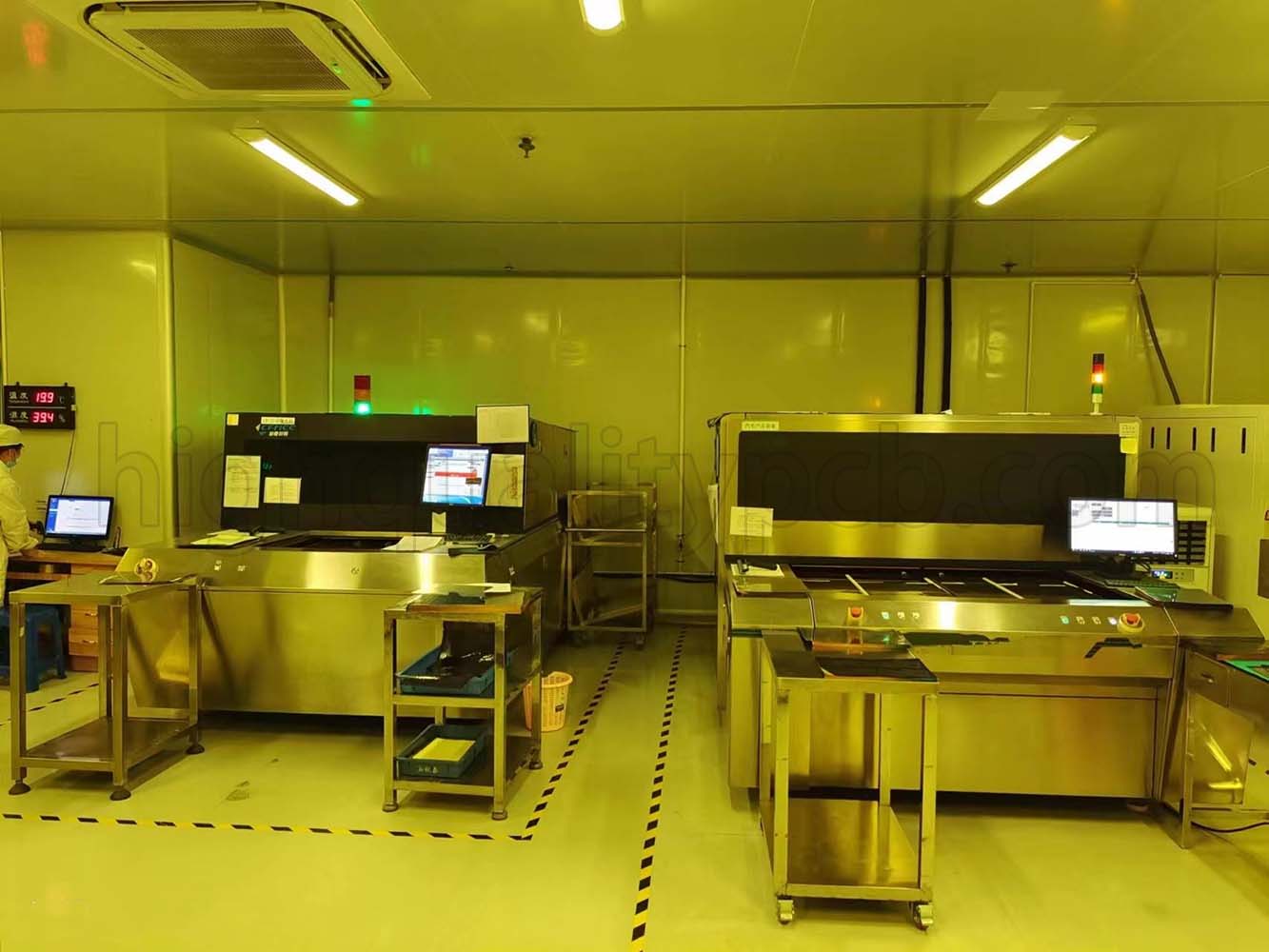
Development: Use sodium carbonate solution to dissolve the unexposed dry film to form a dry film
pattern.
Etching: The copper foil not protected by the dry film is etched away to form a circuit.
Stripping: Remove the exposed dry film on the protective circuit. The developing, etching, and stripping
equipment is a horizontal DES line.
Pre-treatment of covering film: the effect and method are the same as those of pre-treatment of dry
film;
Paste the cover film: align the cover film with the marking line. Then, paste the cover film on the
board and use high heat to pre-fix the cover film. The cover film plays an insulating and protective
role on the circuit. The equipment includes an automatic cover film laminating machine, iron, etc.
Pressing and curing: Through high temperature and high-pressure pressing and high-temperature baking,
the glue between the covering film and the board is cured to achieve the purpose of close bonding
between the two. The primary equipment includes a pressing machine and oven;
Surface treatment: Flexible printed circuit surface treatment mainly includes immersion gold or gold
plating. According to customer requirements, metals such as nickel and gold are deposited on the exposed
pads of FPC using chemical or electroplating principles. It protects the pads and maintains their
solderability.
Electrical testing: Check whether there are open short circuits or four-wire defects through mechanical
equipment. The primary device is an electrical testing machine and a flying probe tester.
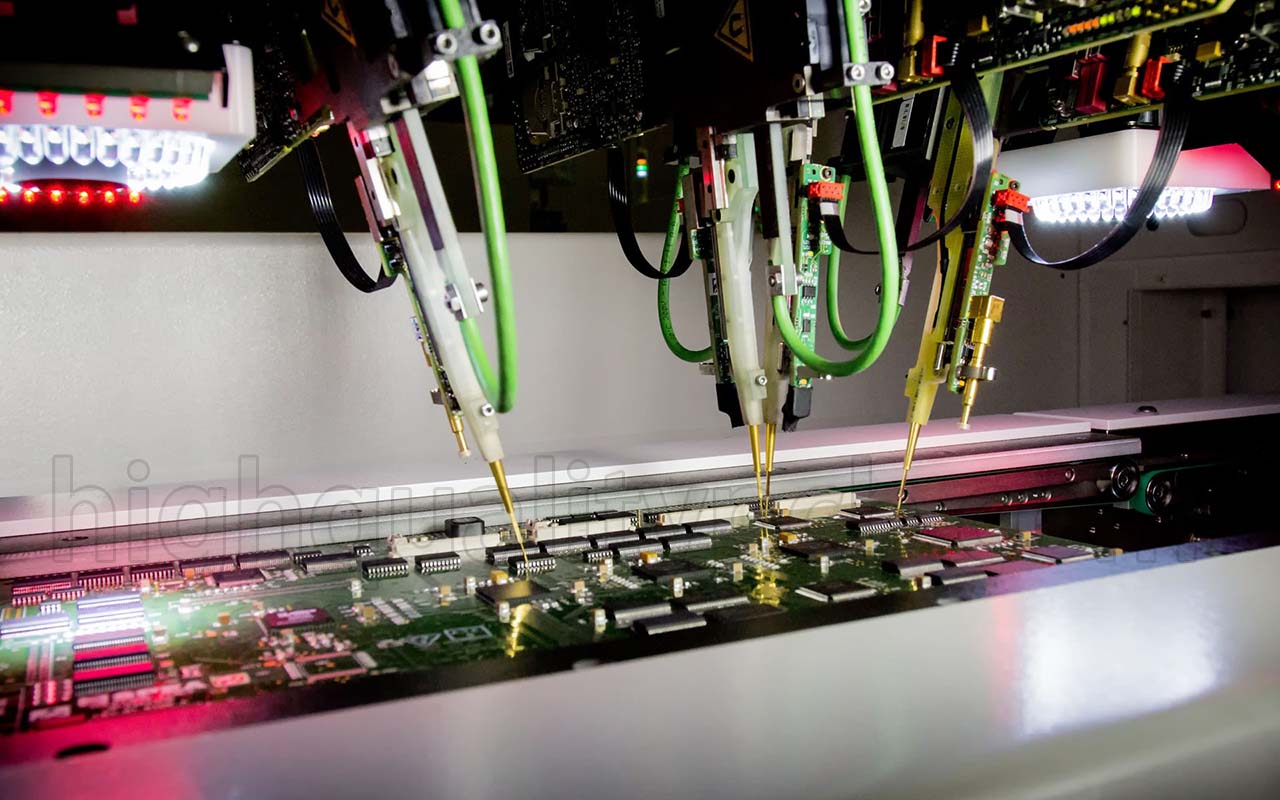
Assembly: According to the alignment markings or hole positions, the reinforcement or electromagnetic
film is attached to the product. The equipment includes automatic reinforcement and laminating machines,
soldering irons, irons, etc.
Silk screen printing: Printing text ink onto products through the screen printing principle, mainly
printing product models, production cycles, various component logos, etc. The primary equipment includes a
silk screen printer, oven, text inkjet printer, etc.
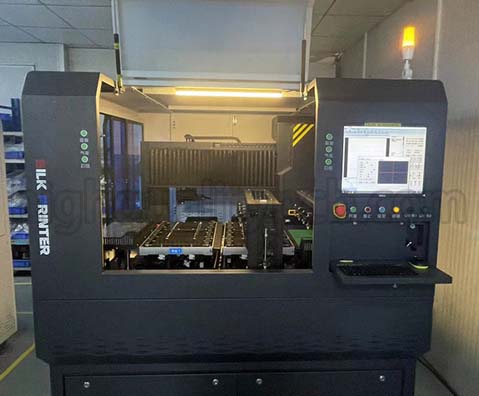
Molding: The final product shape of the customer is formed through mechanical or laser cutting. The
equipment is a laser-cutting machine.
Final check: Check the appearance and surface condition of the product through manual visual inspection
and equipment to separate good products from defective products.
Perform reliability testing on the product to confirm whether it meets customer requirements. The
equipment includes CCD, AVI, reliability testing equipment, etc.
From the above introduction of each production process, we can be seen that FPC production requires
different technologies.
The production process is cumbersome and difficult. Therefore, compared with
ordinary PCB, the manufacturing cost of flexible circuit boards is higher. And it takes more time.
However, FPC's excellent flexibility, lightness, and reliability, FPC provides more possibilities
for equipment and products in many fields. And it is increasingly favored by engineers.
Rigid-PCB vs Flexible PCB
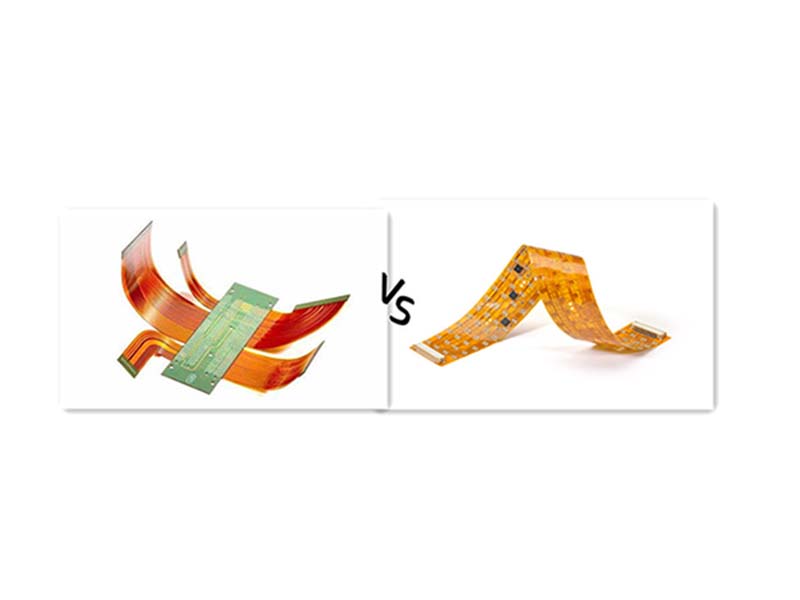
1) Base material
They use different substrates. Rigid circuit boards use glass fiber and epoxy resin, while flexible
circuit boards use polyester film or polyimide.
2) Plasticity and bendability
Flexible circuit boards have good bendability, can be folded and bent at will, and have strong
plasticity. Rigid circuit boards cannot be bent and are used to arrange and stabilize electronic
components.
3) Applicable scenarios
flexible printed circuit board is primarily used in flexible circuits, such as flexible displays,
automotive panels, and other products that need to be folded, bent, and reduced size. PCB is suitable
for general circuit boards of various specifications, such as control circuit boards, audio circuit
boards, signal circuit boards, etc.
4) Features
Advantages of flex-PCB: lightweight, small size, can be used in a smaller space; high reliability, can
withstand bigger bending and folding.
The disadvantages are high cost and complex manufacturing process; strong plasticity, easy accumulation
of static charge, and prone to short circuits and failures.
The advantages of PCB: PCB assembly is simple and stable. Manufacturing costs are low. A high degree of
automation can improve production efficiency.
The disadvantages are large size, heavy weight, not resistant to falling, and limited space structure.
In summary, different types of circuit boards have their advantages and disadvantages. So, we consider
which circuit board to choose based on our product requirements, cost, performance, and environmental
protection. Then, the PCB manufacturer will produce it.
Application of flexible circuit boards
Flexible printed circuit board is widespread in many fields due to its excellent characteristics. The
specific applications are as follows:
1) Consumer electronics
In consumer electronics, flexible circuit boards are widely used, such as smartphones, laptops, etc.
Taking smartphones as an example, they can achieve highly integrated design, making the phone thinner,
more beautiful, and more reliable.
2) Medical field
Flexible circuit boards are used for internal connections of wearable devices, medical instruments, and
other products to improve the comfort and portability of the equipment.
3) Car
In the automotive field, flexible circuit boards can cope with complex circuit layouts and vibration
environments, improving the safety and reliability of automobiles.
4) Aerospace
In aerospace, flexible circuit boards have become a vital choice for internal circuit connections in
aircraft due to their lightweight and high reliability.
What to Consider When Choosing a Flex-PCB Manufacturer?
Some questions you need to ask before choosing a flex circuit manufacturer:
• What are the specifications of your flexible circuit board, and can the manufacturer meet them?
• Is the Flex-PCB manufacturer a professional proofing, small batch, or mass processor?
• Does the flexible printed circuit quality meet your requirements?
• Does your FPC budget cost match the manufacturer's quotation?
• How quickly can FPC manufacturers deliver products?
Highqualitypcb has been working in the PCB industry for 12 years. We provide you with one-stop PCB
assembly services. You can trust highqualitypcb with everything from component procurement to PCB
assembly. We have a professional technical team and multiple PCB factories and PCB suppliers. If you
need any PCB services, you can contact us.