Ultimate Guide to PCB Assembly Costs in 2025
PCB assembly costs are driven by complexity, components, volume, region, and processes. Optimizing these cuts expenses, boosts efficiency, and improves quality.
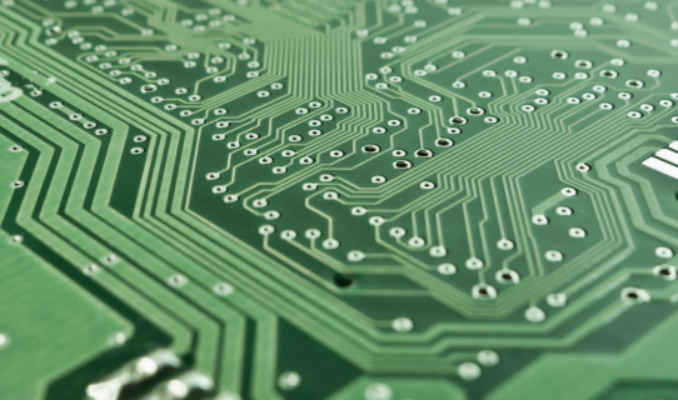
Table of Content
Have you got questions about PCB Assembly cost? Accurate estimations of PCB assembly are essential. Knowing this can reduce your costs.
This guide will help you to make informed decisions about reducing PCB assembly costs.
1. 8 Key Factors Influencing PCBA Cost
1.1 PCB Complexity
(1)PCB Layers
Single-layer PCBs and double-layer PCBs are the cheapest. Due to their complexity in routing and the higher costs of materials, multilayer PCBs tend to be more expensive. According to general belief, the cost of PCBs increases as layers increase.
(2)Dimension PCB
Cost is determined by the size of a PCB. The larger the PCB panel, the more space is available to add circuits and components for its intended use. Since they can be used in large to medium devices, larger PCBs tend to be more expensive. Smaller PCBs can be cheaper and use fewer components. The assembly costs in the factory increase as the PCB gets larger.
(3)PCB Minimum Hole Diameter
Drillig requires a drill bit. Standard drill bits cost less than drill bits of smaller diameter. When the hole diameter is small, drilling costs increase.
(4)Trace Width
To achieve narrower gaps or traces, we will need to use advanced laser drilling techniques or specialized etching methods. Tooling and production costs will increase accordingly.
(5)PCB Thinness
Assembly costs increase with board thickness. The drilling of holes into large boards requires complex equipment and precision. Customized assembly panels will be needed for PCBs that are not standard sizes, increasing costs.
(6)PCB Substrate Materials
The substrate material used for the PCB can have a significant impact. Materials such as FR-4 can be inexpensive and common. Specialized substrates such as ceramic or flexible materials may be more costly.
(7)PCB Solder Mask Color
Standard colors, like green, are the least expensive. Custom colors are more expensive.
(8)Surface Finishes for PCBs
Different PCB surface finish methods result in different costs.
- HASL: A low-cost but less precise technique.
- Impression silver/tin: It is a reasonable price. The boards are limited in shelf life and can impact inventory and assembly times.
- ENIG: The gold plating is the reason why ENIG is at its highest. This is ideal for high-reliability or wire bonding applications. Immersion gold costs more, and the thicker we make it.
1.2 Components And Bill of Materials (BOM)
The Bill of Materials (BOM) and the component selection are key factors in determining PCB Assembly costs.
(1)Purchase of Components Price
During shortages, we may have to spend more on components. The BOM cost will be dramatically increased accordingly.
Components from famous brands can be more expensive than components from other brands. Their products are safer, and they perform better. Orinew components are original.
(2)Quantity and Density of components
Every additional component increases the time to pick and place. Boards that have a large number of components require additional programming time on the machine and may even need nozzle replacements. This results in higher labor costs and depreciation.
Design and placement rules are stricter for components that are densely packed. The result is increased rework and a reduced yield.
(3)Component Type & Packaging
Surface Mount (SMD)assembly costvs Through Hole (THD) assembly cost
SMD component assembly is usually less expensive. Because the automatic placement machine can quickly process a large number of components, greatly improving production efficiency.
Soldering through-hole components is done using wave soldering or manual soldering. These require extra steps such as inserting the lead into holes. These increase labor costs and time.
Package complexity andassembly difficulty
BGA/LGA/Flip-Chip: These high-density packagings require precise placement, solder joint inspection by X-ray, and underfilling. Inspection costs and special processes can be increased per board.
Components that are not standard shapes may require manual positioning or special tooling. This results in increased setup costs and decreased production speeds.
1.3 Order Quantity
The price per PCB will depend on the number of boards we order.
- Wecan expect to spend a lot of money if our only requirement is a small number or prototypes. Additional setup fees will apply. Orinew charges RMB 200-300 for small batches;RMB 300-400 for medium batches; RMB 500 for larger batches.
- Forbulkorders, the unit price will be lower. We don’t need to pay the engineering fee mentioned above. The price per unit decreases as we increase the number of units.
1.4 Assembly Processes and Technology
(1)SMT Processing Cost
- Stencil Cost and Model Cost: Weneed to understand that there is also a charge for stencil fabrication.When we order in bulk, we will be charged the cost of test fixtures and models.
- SMT placement cost: The cost of the patch is determined by the number of solder points. The more soldering points, the higher the price. Machine placement is more cost-effective in the long run.
(2)Cost of DIP Post Welding Processing
The number of holes also affects the price. As the number of holes increases, so does the price. Two different pricing scenarios exist.
- Wave soldering:The circuit board can handlehigh temperatures up to around 250 degrees. This allows operators to use machines for soldering.
- Manual soldering:The circuit board cannot withstand the high temperatures of wave soldering. Its components must also be soldered manually. This incurs labor costs. In comparison, wave soldering is cheaper.
(3)Cleaning of PCB
In the short term, it may be cheaper to not clean. But residues may affect subsequent testing, increasing rework costs. On the contrary, cleaning the PCB will increase short-term costs. But it is beneficial for later inspection. It can also reduce the rework rate.
(4)Input Program Testing
Sometimes, we provide our own test software to assembly plants. Included in this is the loading of software programs, functional verification, system debugging, and so on. The test may require additional equipment or labor. The cost of labor and equipment will go up.
1.5 Inspection & Testing
PCB assembly requires testing and inspection processes, even though they cost a lot. The tests we generally mention include X-Ray test, AOI, power-on test, FCT, and other indispensable testing. Testing helps to find problems quickly and avoid a lot of rework later.
1.6 Hidden Fees
(1)PCB Depaneling Cost
There is also a cost to separate PCBs from the panel structure. This cost is determined by factors such as board thickness.
- Thicker PCB substrates generally incur higher depaneling costs.
- Standard layouts typically cost less to depanel than intricate shapes.
- Depaneling standard PCB materials generally costs less than high-performance substrates.
- Low-volume production usually costshigher per-unit depaneling costs compared to high-volume batches.
(2)Package Price
Protective packaging solutions like anti-static bags entail expenses as well. For large-scale orders, customized packaging designs typically come with higher expenses. Manual or automated sorting and labeling operations will generate additional costs. There are also costs related to developing packaging that complies with industry standards (e.g., IPC Standards).
(3)Logistics Expenses
Logistics costs encompass both domestic and international transportation. Prices are influenced by multiple factors such as distance, weight, volume, and delivery speed.
(4)Lead Time Expenses
Standard pricing applies to orders with regular processing times. Rush orders frequently involve additional fees due to accelerated handling.
2. 5 Proven Strategies to Reduce PCB Assembly Costs
Now that we understand the cost breakdown of PCB assembly. Let’s explore strategies to reduce expenses without compromising quality.
2.1 DFM Optimization
(1)Layer Optimization: Streamline circuit design by minimizing the number of PCB layers. Balance functionality with layer count to achieve cost efficiency.
(2)Avoid exotic features: Limit HDI or controlled impedance, blind/buried vias to critical areas. Opt for standard FR-4 substrates over specialized materials where feasible.
(3)Component Uniformity: Select common SMD package sizes. Reduce stencil complexity and changeover costs during assembly.
(4)Ensure Adequate Spacing: Maintain adequate spacing between components. Soldering and AOI inspection are made easier, reducing the chance of rework.
(5)Panel Design: Increase the number of panels, and improve material usage. This will reduce costs.
2.2 Cost Control for Bill of Materials (BOMs)
(1)Dual-Sourcing Strategy: Qualify 1-2 alternative suppliers for critical components. It can mitigate price fluctuations and supply chain disruptions from sole-source vendors.
(2)Tolerance Optimization: Select passive components that have a slightly larger tolerance when performance permits. This can reduce component expense.
(3)BOM Standardization: Minimize component diversity by leveraging common parts. It can streamline procurement and reduce inventory overhead.
(4)Bulk Procurement: Aggregate material requirements across projects to meet supplier MOQs. This enables volume discounts through centralized purchasing.
2.3 Process Improvement
(1)Assembly Simplification:
Opt for full SMT designs over THT components where feasible. Eliminate manual/wave soldering to reduce labor and equipment costs.
(2)No-clean Soldering:
Use lead-free solder paste to eliminate post-soldering cleaning steps. It can reduce both cleaning costs and production time.
(3)Test Fixture Standardization: Replace custom ICT fixtures with universal test platforms. Lowers upfront test setup costs and speeds up debugging.
(4)Risk-Based Testing: For low-risk products, perform AOI on sampled boards instead of 100%. Balance quality assurance with cost efficiency.
2.4 Collaborate with Full-Service Manufacturers
Understanding PCB assembly cost drivers is critical. Partnering with excellent PCB assemblers ensures quality and on-time delivery. Success hinges on selecting an experienced, reliable assembly partner.
(1) One-stop Service Advantage: Prioritize manufacturers offering integrated PCB fabrication and PCBA manufacturers. Quality-controlled processes they offered reduce risks of product failures and rework.
(2) Strategic Sourcing: For high-volume orders, Chinese manufacturers always offer cost-effective solutions. Orinew delivers competitive pricing without compromising standards. For small/urgent orders, local suppliers minimize lead times and costs.
2.5 Optimized Packaging and Logistics
(1) Packaging Standardization: Replace custom trays with generic ESD bags for non-fragile PCBs. It reduces packaging costs without compromising ESD protection.
(2) Strategic Shipping: Opt for sea/rail freight over air shipping for bulk orders. This cuts transportation costs significantly for non-urgent deliveries.
3.Mitigating Common Risks
(1)Overlook Hidden Costs: Avoid underestimating expenses like testing, certification, and compliance. These “invisible” costs often exceed 15% of total assembly fees.
(2)Quality-Cost Tradeoffs: Low-cost suppliers may increase long-term expenses via defect rates. Prioritize vendors with proven quality management systems (ISO 9001).
(3)BOM Accuracy: Ensure bill of materials (BOM) completeness to prevent delays.
Use automated BOM verification tools to reduce errors.
(4)Process Optimization: Avoid over-automation for small batches; manual assembly is cost-effective. Mixed SMT+THT boards require dual-line setups, causing 2+ hours/day of downtime.
4.PCB Assembly Costs FAQs
5.Summary
Keep in mind: the lowest-cost choice doesn’t always deliver the best results. Weigh costs against quality standards, delivery deadlines, and long-term performance. It can make informed decisions for our project. Wishing us successful, cost-effective PCB assembly projects now and in the years ahead!
related Posts
Contact us
WhatsApp: +86-18123905375
Wechat: +86-18123905375
Skype: ali_youte
Email: sales@highqualitypcb.com