Comprehensive Guide to PCB Surface Finish in 2025
PCB surface finish protects circuits, enhances solderability & extends lifespan. Choosing the right coating is crucial for durability.

Table of Content
PCB is the backbone of the electronics industry. People can’t live without PCBs. PCB surface finish is one of the most important parts of manufacturing a PCB. Choosing the right one can effectively improve the performance, durability, and compliance of the PCB.
In this article, we will take a deep look at the different types of PCB surface finishes. Moreover, we can learn how to choose the right PCB surface finish for your board.
1.What Is PCB Surface Finish?
First, let’s briefly learn about PCB surface finish.
In essence, a PCB surface finish is a protective layer applied to copper traces on PCBs. It can enhance PCB’s functionality, reliability, and lifespan. It also enables reliable soldering by promoting strong solder joints.
Each finish type has unique traits. It can make PCB better suited for specific applications. Most surface finishes support fine-pitch component assembly. They also prevent issues such as solder mask shifting and tombstoning.
2.Why IsAPCB Surface Finish Important?
PCB surface finish is critical to PCBs. Without it, copper surfaces will oxidize and corrode rapidly when exposed to air and moisture. This will lead to catastrophic PCB failures. Besides, PCB surface finish determines the performance, reliability, and life of electronic devices.
They serve as a critical barrier between the exposed copper traces and soldered components.
Here’s why PCB surface finishes matter:
2.1 Solderability
It refers to the surface’s ability to form strong, reliable joints during assembly. Different finishes affect soldering ease, directly impacting assembly efficiency and joint quality.
2.2 Surface Flatness
A smooth and uniform surface finish is essential for fine-pitch components and high-quality soldering. Its flatness can enhance electrical performance and simplify manufacturing.
2.3 Connector Longevity
In applications with frequent connector plugging/unplugging, the finish matters. Hard or soft gold finishes provide excellent durability for reliable connections.
2.4 Corrosion Protection
PCBs are vulnerable to corrosion in humid or harsh environments. The surface finish acts as a protective layer of a PCB. It can effectively prevent long-term oxidation of copper traces.
This is vital for maintaining electrical integrity.
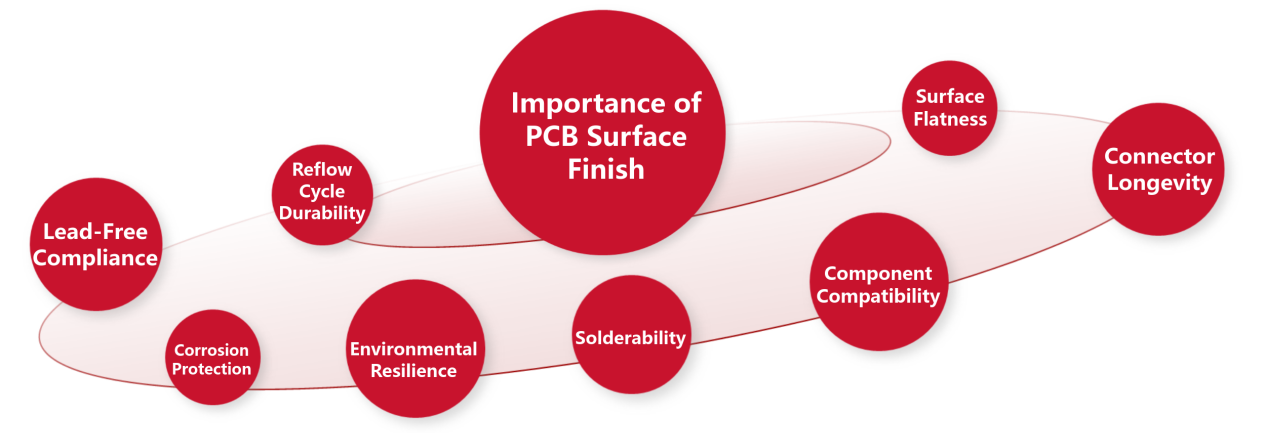
8 Key Aspects of The Importance of PCB Surface Finish
2.5 Lead-Free Compliance
Stringent regulations mandate lead-free finishes to reduce hazardous substances. Options like lead-free HASL or ENIG offer eco-friendly solutions.
2.6 Reflow Cycle Durability
For applications requiring multiple reflow soldering cycles, the finish must withstand repeated heat exposure. ENIG (Electroless Nickel Immersion Gold) is known for its reflow resistance.
2.7 Environmental Resilience
Environmental factors like moisture, temperature swings, and chemicals can degrade PCBs. Choosing the right finish based on operational conditions ensures sustained reliability.
2.8 Component Compatibility
The finish ensures a level PCB surface. It is critical for the precise placement of fine-pitch components. This improves electrical conductivity and production yield.
3.What Are The Types of PCB Surface Finish?
Before you choose a PCB surface finish, understand that it is key. You must choose the one that is best for your project. They all have pros and cons.
We will now discuss in detail the different types of surface finishes. Let’s explore these finishes in detail:
3.1 Hot Air Solder Level (HASL)
HASL is the most popular and affordable surface finish. Its process is simple. Dip the bare PCB in the molten metal. The solder is applied over the copper to remove it from the tank. The PCB surface is then leveled with hot-air knives. This creates a soldering-friendly surface.
HASL works well with SMTs and large components. If the SMTs are smaller, they will not perform as expected. This is not compatible with Fine Pitch Technology. The processing temperature ranges from 260-270℃. Because of the high temperatures, defects may occur on the circuit boards.
Remember that it contains a lot of lead. The lead in the alloy is carcinogenic. It’s typically dipped into tin-lead. It’s therefore not RoHS compliant.
3.2 Lead-free HASL
Lead-free HASL works similarly to traditional HASL but without lead content. It can be used in many ways without worrying. And it complies with RoHS standards. It retains the same pros and cons as traditional HASL.
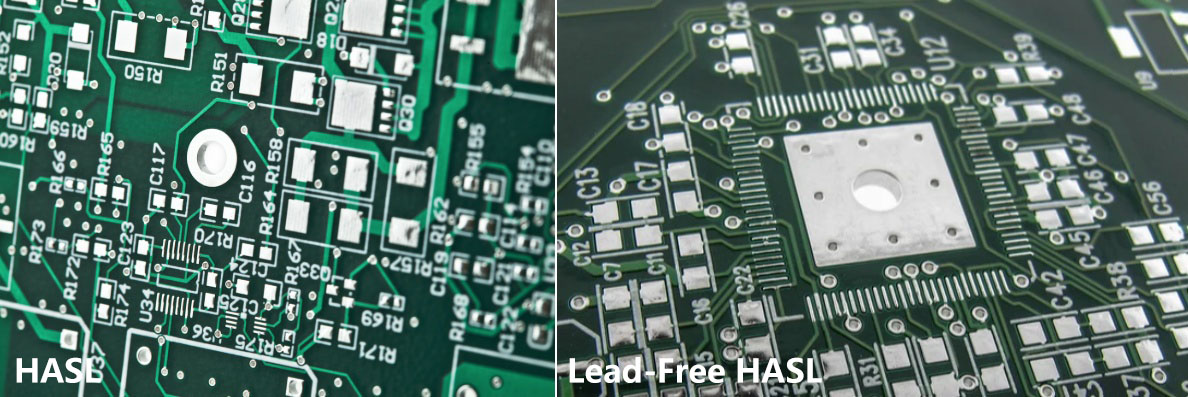
HASL VS Lead-Free HASL
3.3 Immersion Tin
Immersion Tin is a surface finish that is free of lead. It is also ideal for small components. The finish is flat and very thin, making it excellent for Fine Pitch Technology.
This PCB surface finish is cost-friendly but also has some disadvantages. Tin can react and reduce the shelf-life of PCBs. It is also susceptible to tarnishing, so you should use it as quickly as possible. It is very sensitive. You will see tin whiskers on the printed circuit board after a few months. All current solders are made of tin so the tin can be used with any solder.
3.4 Immersion Gold
Hard Gold is another name for Immersion Gold Surface Finish. This is a costly surface finish using a layer of gold on the PCB. This is done by electroplating and a layer of hard gold is applied to the copper surface. The PCB adheres to the layer firmly, increasing the board’s strength. Gold is a good conductor and therefore has excellent electrical performance. Its oxidation resistance also makes it a great choice. The surface finish is perfect for PCB areas, which are subject to high wear. The surface finish can last a very long time.
This type of surface finish is associated with extra processing and high prices. Its price is related to the thickness of the immersion gold. The thicker the immersion gold, the higher the cost. The surface finish is difficult to process. It is rarely used due to its high cost, but it is indeed a great surface finish. Hard gold has poor solderability.
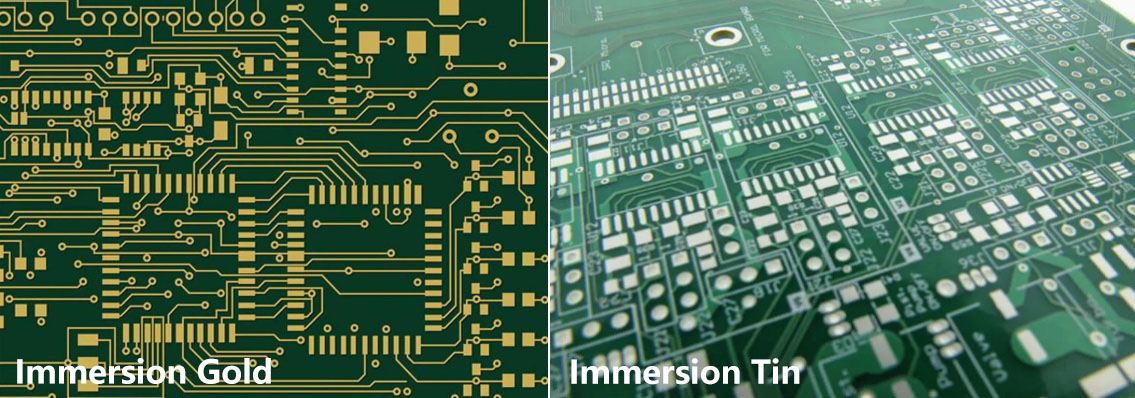
Immersion Gold VS Immersion Tin
3.5 Immersion Silver
The cost of immersion silver is reasonable. It’s a flat finish, and the copper is protected from oxidation by silver plating. The silver layer is thin but has excellent conductivity. It does not change the size of the hole, which is good for Fine Pitch Technology.
This type of surface finish has a problem: tarnishing. Silver plating will tarnish when it is exposed to the air. It is packed in anti-tarnish packaging as soon as it can be to prevent tarnishing. The silver is extremely sensitive and you must solder it after removing it from the package. Immersion silver has a moderate life. The cost is low and it meets RoHS standards.
Immersion silver is a process that falls between OSP, electroless nickel, and immersion gold. It is a relatively simple and fast process. Even if the PCB has been exposed to pollution and humidity or heat, it can still retain good solderability. However, its luster will be lost. Immersion silver is not as strong as immersion-gold/electroless nickel because it does not contain nickel.
3.6 Organic Solderability Preservatives
OSP is the process used to finish the copper foil on printed circuit boards. It meets the RoHS directive requirements. OSP stands for organic solvency preservatives.
OSP is resistant to moisture, heat shock, and oxidation. It protects copper surfaces from further corrosion (vulcanization, oxidation, etc.) under typical conditions. In the high-temperature weld process, however, the protective film needs to be removed quickly and easily by the flux. Only by this can the exposed clean copper surface be combined immediately with the molten metal solder to quickly form a solid solder joint.
A water-based finish protects copper in this type of surface finishing until it is soldered. This coating increases the life of copper by preventing oxidation. It’s not as durable on organic surfaces and is quite sensitive. It is a very short-lived product.
OSP is a cost-effective surface finish. The process is simple and takes less time. The coating does not affect the size of holes on the PCB. It has a flat, excellent surface and is eco-friendly. It is suitable for areas where PCBs are handled with care, as there is less wear and tear.
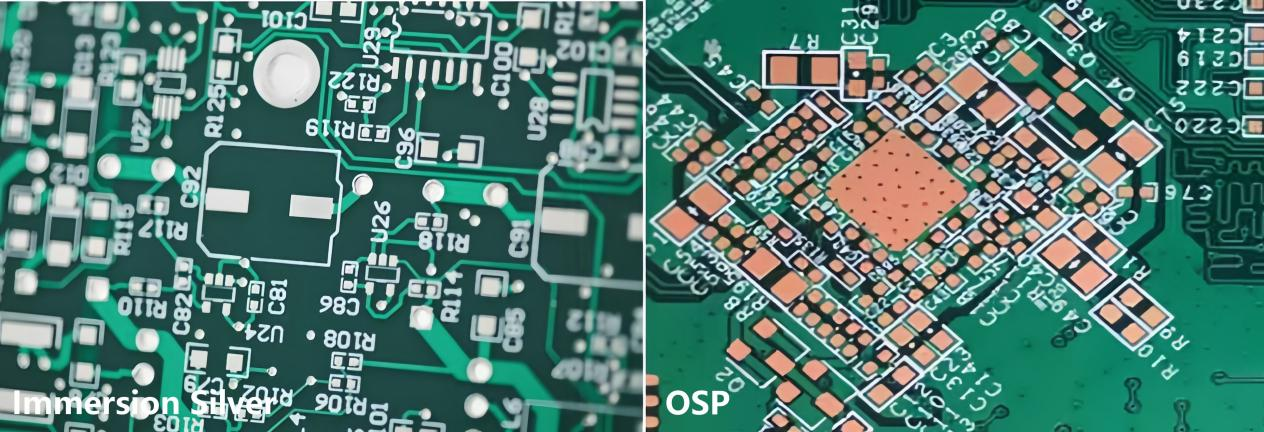
Immersion Silver VS OSP
3.7 Electroless nickel immersion gold (ENIG).
ENIG is most commonly used due to its RoHS compliance and properties. The nickel is thickly layered on the copper, and then a thin gold layer is placed over it. The components are firmly soldered to the nickel, and a thin layer of gold protects it until the soldering process is complete.
ENIG is durable and offers a long shelf life. It’s pricey because it has two layers, especially gold. The surface is flat and thin, with a finish that allows it to be used on smaller components. The only problem that ENIG has is black pad syndrome. This is caused by the buildup of phosphorus in between the gold layer and nickel layer.
3.8 Electroless Nickel Palladium Immersion gold (ENEPIG).
ENEPIG has the best surface finish for preventing corrosion and air reactions. It is the best for its long shelf life as well. This kind of surface finish is made up of three layers, including nickel, palladium, and gold. They work together to provide long-lasting performance.
Unlike ENIG, there is no black pad syndrome with ENEPIG. RoHS-compliant and free of lead, it is a great product. The main problems with ENEPIG are its complex processing and high price.
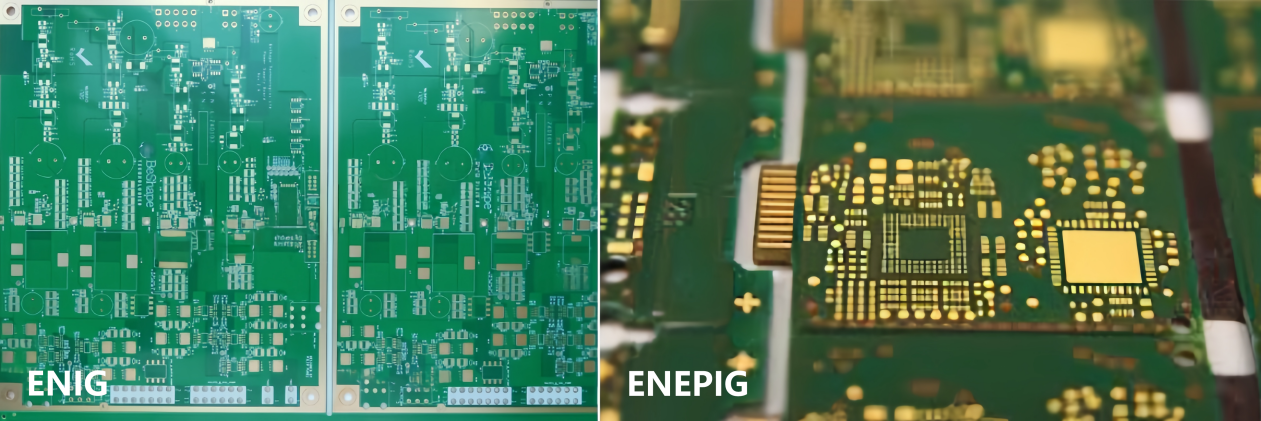
ENIG VS ENEPIG
In addition to the above treatment methods, you can also use a variety of mixed processes. A mixture of two or more surface finishes is used to achieve the best performance. One PCB can have more than one surface finish. The most commonly used surface finishes include ENIG + OSP and ENIG+HASL.
The following is a table of PCB surface finishes.
Type | Advantages | Drawbacks | Ideal For |
HASL | Most popular, affordable, soldering-friendly surface | Non-uniform surface, high thermal stress, environmental concerns (uses lead) | Large components, SMT parts |
Lead-free HASL | RoHS compliant | Non-uniform surface, high thermal stress | Same as HASL |
Immersion Tin | Good solderability, reasonable, flat surface | Prone to oxidation, limited durability in harsh conditions. | Small components and fine-pitch technology (FTP) |
Immersion Gold | Premium finish, electrical performance, enough hard | High cost, complex processing, poor solderability. | Connectors and high-wear applications |
Immersion Silver | Flat, cost-effective, good solderability, | Sensitive to tarnishing, limited harsh-environment resistance | Fine-pitch technology (FTP) |
OSP | Low cost, flat surface, eco-friendly. | Short shelf life, sensitive to handling, limited corrosion resistance. | Quick-turn PCBs, fine-pitch components |
ENIG | Excellent solderability, smooth surface, high corrosion resistance. | High cost, risk of “black pad” defects, longer process time | Tiny components and high-reliability applications |
ENEPIG | Resists corrosion, avoids black pad issues, RoHS-compliant | Costly | High-reliability applications |
Mixed Surface Finish | Optimized performance | – | Widely used |
4.What Are The Key Factors of Selecting A PCB Surface Finish
Consider these key factors when choosing a PCB surface finish:
4.1 Solderability
Reliable soldering is vital for quality assembly. HASL and ENIG typically offer the best solder joint reliability.
4.2 Signal Integrity
In high-speed/high-frequency designs, prioritize flat surfaces and low signal loss. Immersion gold or silver are the top choices here.
4.3 Storage Duration
For long-term storage, pick finishes with extended shelf lives, such as ENIG or immersion silver.
4.4 Cost Constraints
Cost impacts your decision. It should also be a primary consideration. Hard gold offers premium reliability but comes at a higher price. For tighter budgets, immersion silver balances cost and performance. ENIG offers excellent performance but at higher costs, while OSP is more budget-friendly with limited durability.
4.5 Operating Environment
The PCB’s environment dictates the finish choice. You should consider temperature extremes, humidity levels, and exposure to chemicals or gases before making your choice. For harsh conditions, you are opt for durable, corrosion-resistant finishes like hard gold or ENIG.
4.6 Lifespan Requirements
While all finishes extend PCB life, some outlast others. ENIG and immersion gold resist wear from thermal cycling and environmental stress better than softer finishes.
4.7 Application-Specific Needs
The PCB’s function matters. Fine-pitch components demand ultra-flat surfaces—immersion silver or immersion tin are ideal here.
Different fields demand specific finishes. High-frequency applications may require finishes that minimize signal loss. You also prioritize flat surfaces. Immersion silver is the top choice here. Hard gold plating is ideal for frequently mated connectors, thanks to its excellent wear resistance.
4.8 Environmental Compliance
You should ensure the finish meets industry standards. Avoiding lead-containing finishes like HASL if RoHS compliance is required, especially when exporting to regulated regions.
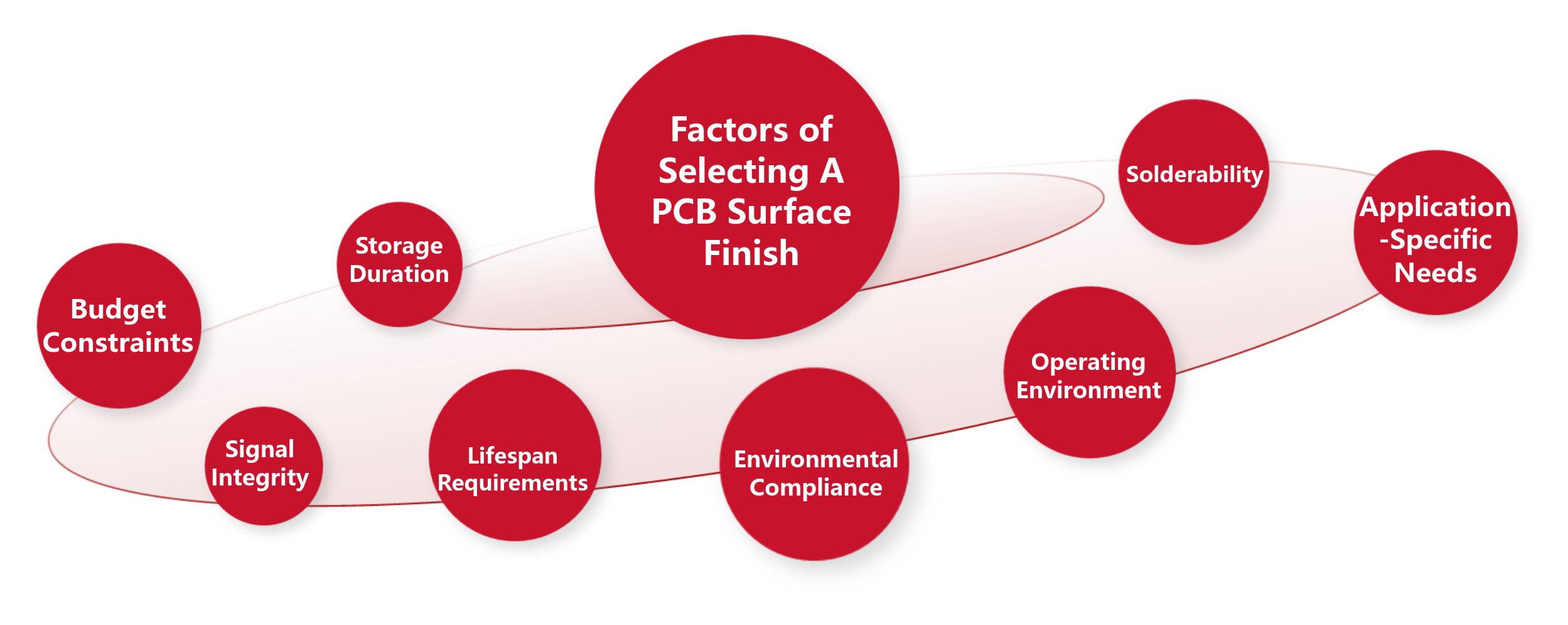
8 Factors of Selecting A PCB Surface Finish
5.PCB Surface Finish FAQs
6.Surface Finish at Orinew
Orinew is a excellent Chinese PCB manufacturer with over 10 years of expertise. We stick to produce every high-quality PCB, all while adhering to strict RoHS-compliant quality control standards.
We offer a full range of surface finish options to meet diverse customer needs,. Whether you require prototypes, PCBs, or PCBA assemblies, we will provide pricing and highly competitive service.
Curious to learn more? Don’t hesitate to reach out—we’re here to help.
related Posts
Contact us
WhatsApp: +86-18123905375
Wechat: +86-18123905375
Skype: ali_youte
Email: sales@highqualitypcb.com